The design of bar candles has undergone modifications over the past decades. Currently used, so-called. third generation, have a very short heating time 2-7 seconds, thanks to the use of a two-part glow wire. Due to the popularization of this type of design in modern cars, it is good to get to know it better.
The new generation bar candle consists of the elements shown in cross section in the drawing. The individual parts of the candle perform the following tasks:
• The threaded end is connected to the regulating spiral and is used to connect the electric supply cable.
• Nickel-plated spark plug body protects it from corrosion.
• The threaded fitting is made on the body by rolling, making it resistant to tearing. In addition, the thread is nickel plated, which protects the spark plug from seizing up in the cylinder head, even after a long period of use.
• The insulator is powdered magnesium oxide, which is also characterized by very good heat conductivity. Compressed during the spark plug production phase, it gives the spirals a fixed position in the glow tube, not allowing them to shift due to vibrations.
• The adjusting spiral is made of nickel alloy or, in newer versions of candles, made of an alloy of cobalt and iron and has this property, that its resistance increases rapidly with increasing temperature. In this way, the current flowing through the heating coil is regulated. Initially, the regulating spiral passes a large current, which allows the heating coil to reach high temperature quickly. Above 400 ° C, the resistance of the regulating scroll starts to increase rapidly and this reduces the heating of the heating coil. Thanks to the regulating effect, the heating time is very short, and the candle temperature does not exceed the temperature limit (around 1100 ° C), which would burn out the glow tube.
• The heating coil is made of a chromium alloy, iron and aluminum. It heats the end of the glow tube to a temperature of about 1000 ° C. Po 2-5 s after switching on, the tube glows almost to the body.
• The weld connecting the two spirals is made with a laser technique, which ensures that the spiral is centered in the tube, thereby evenly heating the entire surface of the candle.
• The heating rod is made of Inconel alloy 601, characterized by resistance to corrosion and aggressive chemical components of gases. The wall thickness is generally 0,7 mm and can be adapted to the characteristics of the engine (mechanical load).
• Double sealing protects the inside of the glow housing from harmful gases, so that the resistance of the helix does not change throughout the service life, which prevents the candle from burning out.
The third generation glow plugs with a two-piece helix were first introduced to the market by Beru. Currently produced diesel engines are already equipped with this type of plugs as standard. Each candle has a spiral length selected in such a way, wire diameter and glow tube, so that the time of switching on and glowing was adjusted to the operating parameters of a given type of engine.
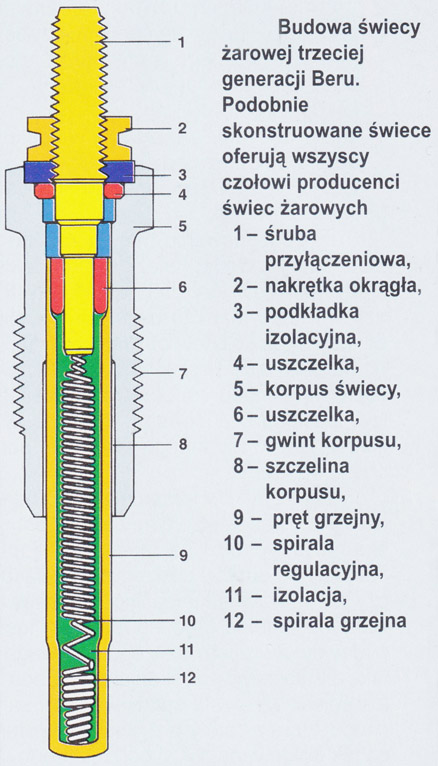